Принципът на производството на високотемпературни турбинни роторни лопатки на авионни двигатели е много прост, но различните параметри в този процес изискват много експерименти, за да се получат параметрите на всеки узел, състава на помощните материали и много късмет.
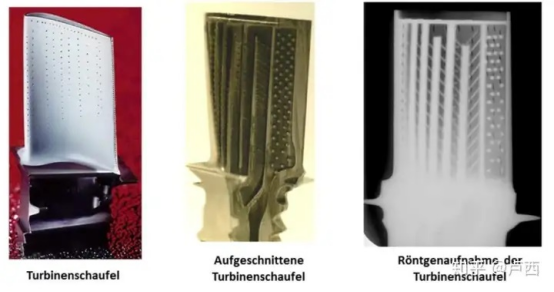
Първо, високотемпературните турбинни роторни лопатки изискват сложни вътрешни охлаждащи въздушни канали (вж. фигурата по-долу). Първо се правят вътрешните охлаждащи въздушни канали (без охлаждащи въздушни отвори, които ще обсъдим по-късно). След това восковият модел се отливане с специална керамика, за да се образуват въздушните канали.
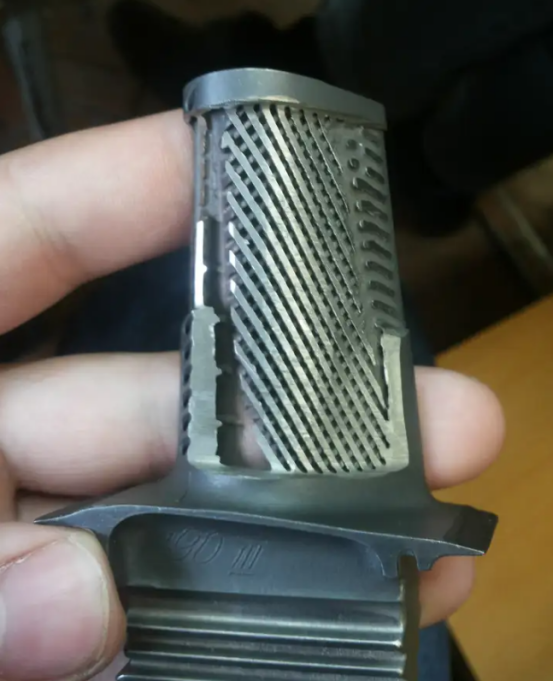
След като получите тази керамична форма за дихалната тръба, съберете я с формата на външната част на лезе и сложете я в отливният печка. Топената свръхалои* влиза в формовото пространство отгоре надолу (включително керамичната форма за дихалната вътрешна тръба и восковата външна форма). Екстремно утежнява да се правят безбройни слоеве на облигации между всяка форма. Немските firми използват роботи за това, а изглежда, че Русия все още използва бабушкини щетки. Тези облигации директно определят качеството на отливката, а допустимостта е екстремно ниска.
В този момент машината за отливка стриктно контролира температурата на топената свръхалои и след това я закрепява на хоризонтална повърхност (тоест, растежа на кристала), отдолу нагоре, когато кристалите растат спираловидно (селектор на кристали), те се изтискват и се избират взаимно, и накрая остава само един кристал, най-близък към предварително зададената посока, и този кристал продължава да расте нагоре.
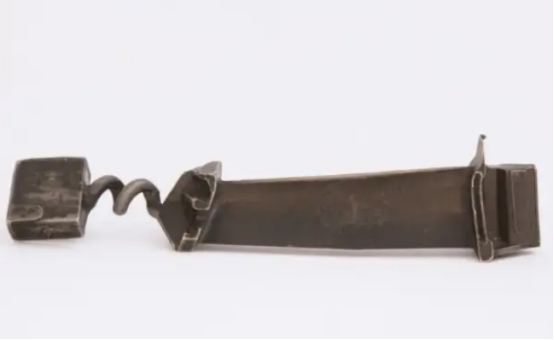
Поради това, че високотоносната ос трябва да се върти повече от 10 000 пъти, всяка част е подложена на над 10 тона центробежна сила, а силата на никеловите кристали във всеки посока е различна, затова нейният диагонал (най-силната посока) трябва да е в рамките на 10 градуса от посоката на центробежната сила. (Ще добавя още нещо - едносмуката никелова алой, използвана в ротора на нискотоносния турбинен rotor, изисква посока на кристалите, но не само един кристал, защото температурата на плавене на единичния кристъл е с 50K по-висока от тази на поликристалните (включително едносмуките)).
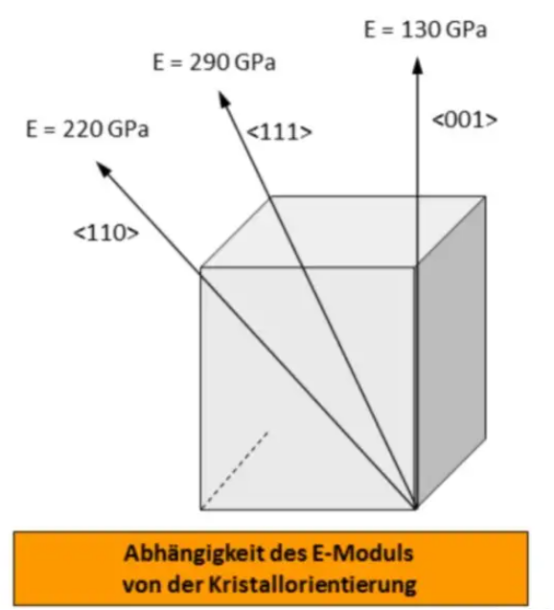
Ефективността не е висока. Колкото ми е известно, много добри немски заводи за прецизно ливене са опитали този процес и най-накрая са станали банкроти. Прагът е наистина прекалено висок.
Накрая, получава се готовият продукт и се използва специално щелък, за да се разтегат керамичните форми останали в каналите за хладене, които правят отворите за охлаждане. Има електрически разтворени отвори и електрохимични отвори. Най-разпространените отвори се правят с лазер. Формата на отворите е също много сложна. След това има електродепозиционно покритие, което също е голямо знание.
Изображението по-долу показва поликристално споделяне отляво, уникато кристал в средата и единичен кристал отдясно.
Обаче, след отливката лопатките нямат въздушни отвори, които свързват вътрешния охлаждащ въздушен канал с повърхността на лопатката. Това обикновено се прави чрез лазер. Защото охлаждащият въздух е изгубил много от своето налягане, когато е изваден от високонатискния компресор и тече от холемият вал до високонатискния турбоз, макар че основният въздушен поток също губи налягане, докато минава през горењето, а процесът от вала до лопатката има определен центробежен компресионен и повишаващ налягането ефект, все още се изисква по-високо статично налягане, за да удари охлаждащия въздух към повърхността на лопатката. В този момент се нуждаем от отвор с разширяващ се пресечен размер, за да обработи охлаждащия въздух, намали динамичното налягане и увеличи статичното налягане, след което охлаждащият въздух отблъсна горещия основен въздушен поток от повърхността на лопатката (много глупости). Повече от това, прекалено висока скорост ще причини охлаждането да бъде директно инжектирано в основния въздушен поток, и има друга задача, която е да образува слой от охлаждаща въздушна филма на повърхността на лопатката, за да защити лопатката, което изисква намаляване на скоростта и повишаване на налягането.
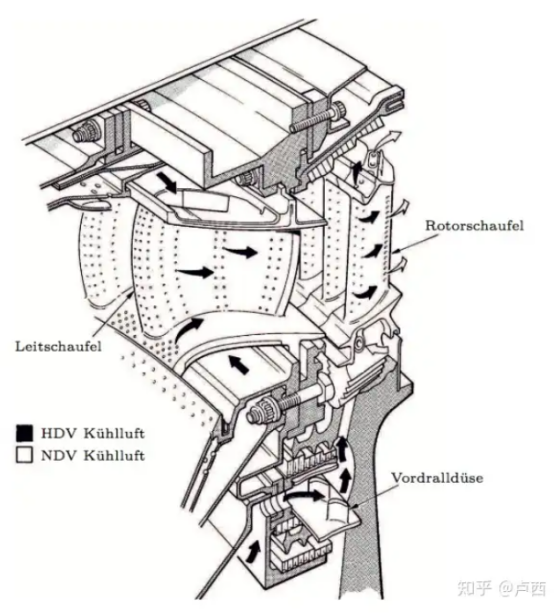
Поради това този тип отвор трябва да оптимизира геометричната си форма за различни позиции. Лазерното пробиване може лесно да се автоматизира, но недостатък е, че ще има вътрешен повърхностен стрес.
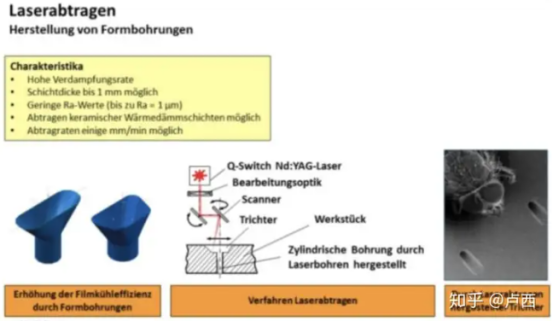
Хвостът на турбинния статор (единично кристално, не по темата) трябва да бъде прободен с пробудителни охлаждащи отвори, за да служи на следващия турбинен ротор. Този отвор е изключително топъл и не може да се справя с вътрешния стрес, затова се прави чрез електрохимична корозия. Разбира се, това не са абсолютни правила, и различните компании имат различни методи на обработка.
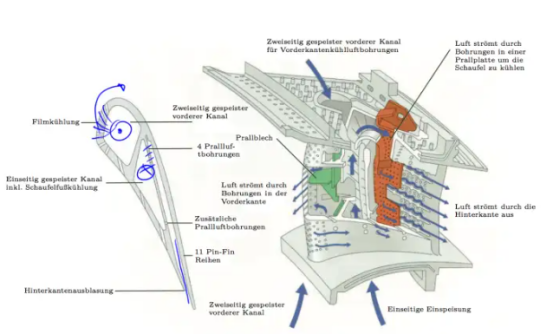
След като направите това, една кристална лопаст на турбина е получена, но още не е обработена. Модерните лопасти на турбини изискват слой от термичен барьерен покрив от циркониев оксид, един вид керамика. Тъй като е керамика, тя е хрупка до някаква степен. Когато турбината работи, ако има малка деформация, целият слой може да се откъсне и лопастите на турбината ще започнат да плават веднага. Това е абсолютно неприемливо за Hangfa.
След това има процес EB-PVD (Електронно-лъчева физическа паревая депозиция), метод на парева депозиция.
Разбира се, преди това има много слоеве от други материали, като например платиново гальvanизиране (платина), плазмено спрейване и т.н. Съществува също така слой, който укрепва цирконията и я прилепя като клей. Разбира се, между всяка компания има малки разлики и те не са статични.
Първо, електронната пушка изпраща електронен лъч, който се води от магнитното поле и достига до циркониевия субстрат. Субстратът, обстрелван от електроните, преминава в газов състояние, а газовият цирконий се насочва към повърхността на лезеца, за да започне да расте. Цирконият ще рaste в малки палчици с диаметър 1 микрон и дължина 50 микрона, густо покриващи повърхността на листата без да се покриват порите. Тъй като това не е цялостен керамичен материал, малките палчици могат да се движеят леко спрямо един друг, без целият слой да се откъсва, което решава проблема с провал при деформация.
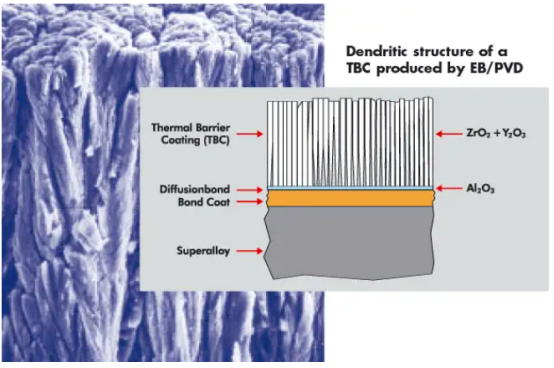
Цирконията има изключително висока твърдост и изключително ниска термична проводимост, което позволява да се постигне много крут температурен градиент между никеловата основа и горещия въздушен поток. С вътрешно охлаждане и въздушно плевелно охлаждане лопатката може да работи дълго време с висока твърдост и висока надеждност в среда, много по-висока от собствената й температура на плавене.
В този момент повърхността на лопатката е готова. За да се вмества в турбинния колело, лопатката също трябва да има чекмеджеподобна или шипова структура на корена.
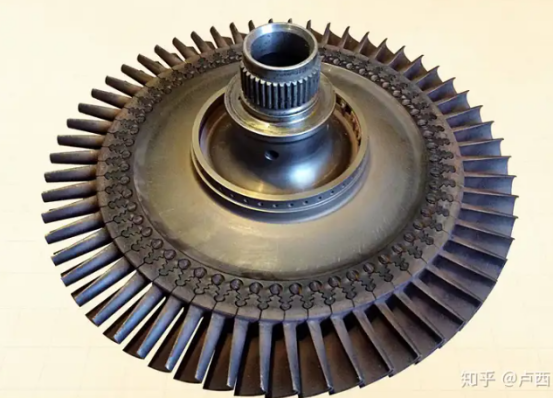
Както беше споменато по-рано, всяка турбинна лопатка притежава над десет тонове центрифугална сила при работа, а и самият корен на лопатката трябва да бъде обработен много точно. Никеловите супералои са много твърди, устойчиви на високи температури и много трудни за обработка.
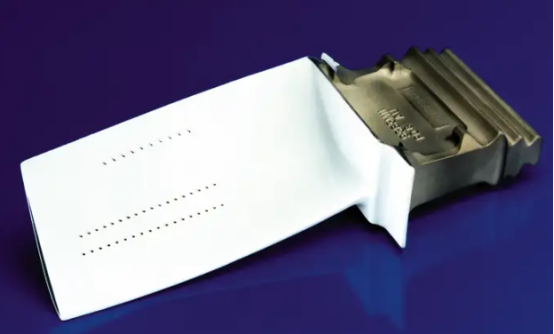
Коренът на лопатката е изгръден. Лопатката е заключена в специален фиксатор, а горните и долните гранични камъни с противоположна геометрия (женски форми) гръзнат вътрешно.
Това ще доведе до бързо изнасяне на шлифовното диски, затова се добавя позитивен диамантен шлифовен диск отвъншната страна на двете шлифовни диска, който постоянно шлифе диска, за да го запази работещ. Индустриалните диаманти на диамантния диск са лепени от роботи.
След тези процеси и проверка, лезето е готово да работи. То е само част от авиационен двигател, а авиационният двигател е само модул върху самолет.