หลักการของการผลิตใบพัดเทอร์ไบน์แรงดันสูงของเครื่องยนต์อากาศยานนั้นเรียบง่ายมาก แต่ว่าพารามิเตอร์ต่าง ๆ ในกระบวนการนี้จำเป็นต้องใช้การทดลองจำนวนมากเพื่อหาค่าพารามิเตอร์ของแต่ละโหนด การผสมของวัสดุช่วย และความโชคดีเป็นอย่างมาก
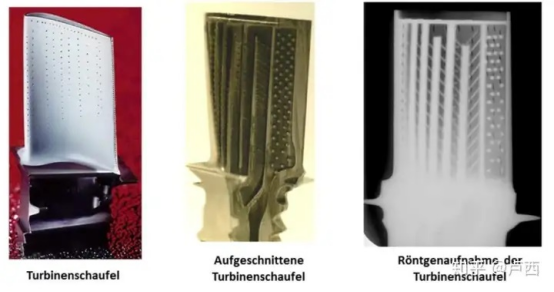
ก่อนอื่น ใบพัดเทอร์ไบน์แรงดันสูงต้องมีท่อระบายความร้อนภายในที่ซับซ้อน (ดูภาพด้านล่าง) ก่อนอื่นจะสร้างท่อระบายความร้อนภายในก่อน (ไม่รวมรูระบายความร้อน ซึ่งจะกล่าวถึงในภายหลัง) จากนั้นหล่อแม่พิมพ์蠟ด้วยเซรามิกพิเศษเพื่อสร้างท่อระบายความร้อน
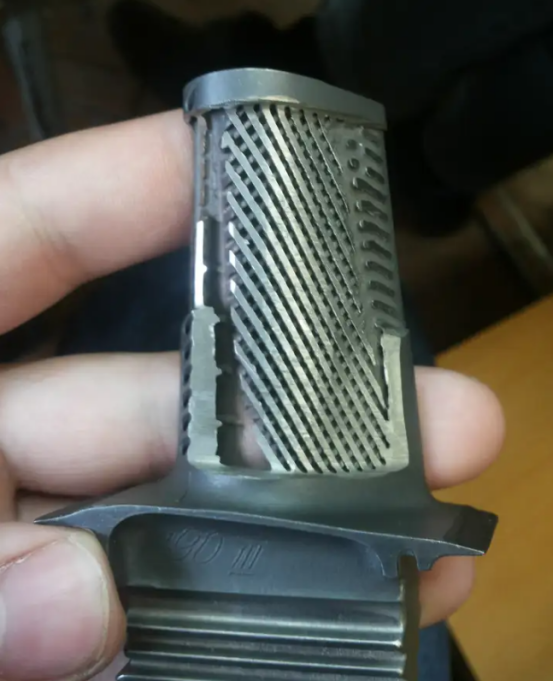
หลังจากมีแม่พิมพ์ทางอากาศเซรามิกแล้ว ให้นำมาประกอบกับแม่พิมพ์นอกของใบมีด จากนั้นใส่เข้าไปในเตาหล่อโลหะ โลหะซูเปอร์อัลลอยที่หลอมละลายจะไหลเข้าสู่ช่องแม่พิมพ์จากบนลงล่าง (รวมถึงแม่พิมพ์เซรามิกสำหรับทางอากาศและแม่พิมพ์蠟นอก) การทำชั้นเคลือบหลายชั้นระหว่างการสร้างแม่พิมพ์แต่ละครั้งนั้นยุ่งยากมาก บริษัทในเยอรมนีใช้หุ่นยนต์ในการทำ ในขณะที่รัสเซียดูเหมือนว่ายังคงใช้แปรงของป้าเหล่านั้น เคลือบเหล่านี้เป็นตัวกำหนดคุณภาพของการหล่อโดยตรง และอัตราความผิดพลาดต่ำมาก
ในตอนนี้ เครื่องหล่อจะควบคุมอุณหภูมิของโลหะซูเปอร์อัลลอยที่หลอมละลายอย่างเคร่งครัด จากนั้นปล่อยให้มันแข็งตัวบนระนาบแนวนอน (ซึ่งหมายถึงการเจริญเติบโตของผลึก) จากล่างขึ้นบน เมื่อผลึกเจริญเติบโตในลักษณะเกลียว (ตัวเลือกผลึก) จะมีการเบียดและคัดเลือกกันเอง สุดท้ายจะเหลือเพียงผลึกเดียวที่ใกล้เคียงกับทิศทางที่กำหนดไว้ล่วงหน้า และผลึกนี้จะเจริญเติบโตขึ้นไป
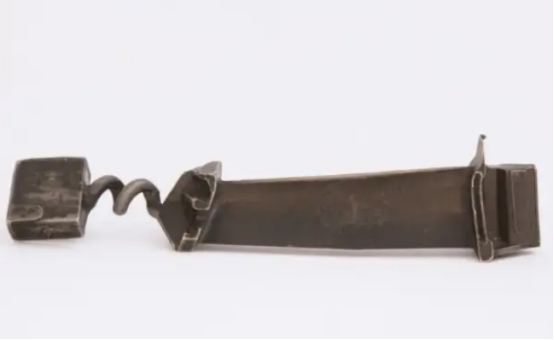
เนื่องจากข้อเหวี่ยงความดันสูงต้องหมุนมากกว่า 10,000 รอบ ชิ้นส่วนแต่ละชิ้นจะถูกแรงเหวี่ยงมากกว่า 10 ตัน และเนื่องจากความแข็งแรงของผลึกนิกเกิลในแต่ละทิศทางแตกต่างกัน ดังนั้น มุมเฉียง (ซึ่งเป็นทิศทางที่แข็งแรงที่สุด) จำเป็นต้องอยู่ภายใน ±10 องศาของทิศทางแรงเหวี่ยง (อีกอย่างที่อยากบอกคือ อัลลอยด์นิกเกิลแบบเดี่ยวที่ใช้ในโรเตอร์เทอร์ไบน์ความดันต่ำต้องการทิศทางของผลึก แต่ไม่ใช่เพียงแค่ผลึกเดียว เพราะจุดหลอมเหลวของผลึกเดี่ยวสูงกว่าโพลีคริสตัล (รวมถึงผลึกเดี่ยวทิศทาง) 50K)
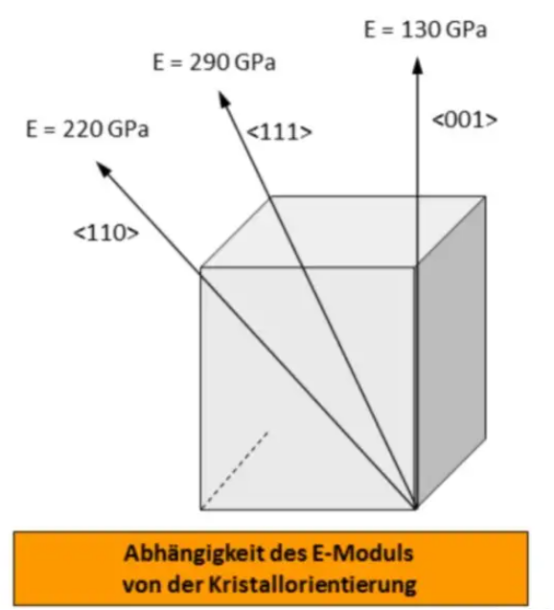
อัตราการสำเร็จงานไม่สูง เท่าที่ผมรู้โรงงานหล่อแม่นยำหลายแห่งในเยอรมนีได้พยายามท้าทายกระบวนการนี้และสุดท้ายก็ล้มละลาย ขีดจำกัดของการทำจริงๆ สูงเกินไป
ในที่สุดจะได้รับผลิตภัณฑ์สำเร็จรูป และใช้สารด่างพิเศษเพื่อละลายแม่พิมพ์เซรามิกที่เหลืออยู่ในช่องอากาศ ซึ่งใช้ทำช่องระบายความร้อน มีช่องจากการละลายทางไฟฟ้าและช่องทางเคมีไฟฟ้า ช่องที่พบบ่อยที่สุดสร้างขึ้นโดยเลเซอร์ รูปร่างของช่องก็ค่อนข้างซับซ้อน นอกจากนี้ยังมีกระบวนการเคลือบด้วยการชุบไฟฟ้า ซึ่งเป็นความรู้ที่ลึกซึ้งมาก
ภาพด้านล่างแสดงโพลีคริสตัลทางซ้าย ผลึกเดียวทิศทางตรงกลาง และผลึกเดี่ยวทางขวา
อย่างไรก็ตาม หลังจากการหล่อ ใบพัดจะไม่มีรูระบายอากาศที่เชื่อมต่อดักต์ระบายความร้อนภายในกับผิวใบพัด โดยปกติแล้วจะทำด้วยเลเซอร์ เพราะอากาศสำหรับการระบายความร้อนจะสูญเสียแรงดันจำนวนมากเมื่อถูกดึงมาจากคอมเพรสเซอร์แรงดันสูงและไหลผ่านแกนวงจรเปล่าไปยังเทอร์ไบน์แรงดันสูง แม้ว่ากระแสอากาศหลัก (core airflow) จะสูญเสียแรงดันเมื่อผ่านกระบวนการเผาไหม้ และกระบวนการจากแกนไปยังใบพัดมีผลของการบีบอัด centrifugal และเพิ่มแรงดัน แต่ยังคงต้องการแรงดันสถิตสูงกว่าเพื่อนำอากาศเย็นไปยังผิวใบพัด ในกรณีนี้ จำเป็นต้องใช้รูที่มีหน้าตัดขยายเพื่อจัดการอากาศสำหรับการระบายความร้อน ลดแรงดันพลศาสตร์ และเพิ่มแรงดันสถิต จากนั้นอากาศเย็นจะผลักดันอากาศร้อนจากกระแสหลักให้ห่างจากผิวใบพัด (มีเรื่องไร้สาระมากมาย) นอกจากนี้ หากความเร็วสูงเกินไป จะทำให้อากาศเย็นถูกฉีดเข้าสู่กระแสหลักโดยตรง อีกหน้าที่หนึ่งคือสร้างชั้นฟิล์มอากาศเย็นบนผิวใบพัดเพื่อป้องกันใบพัด ซึ่งต้องการการชะลอความเร็วและการเพิ่มแรงดัน
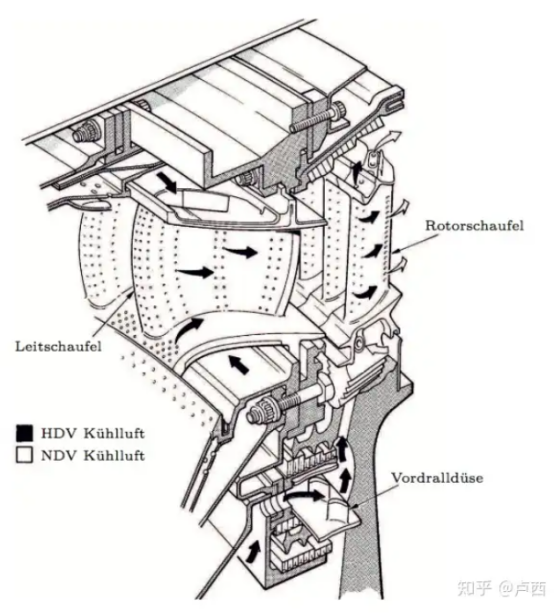
ดังนั้น รูปแบบของรูประเภทนี้จำเป็นต้องปรับให้เหมาะสมตามตำแหน่งที่แตกต่างกัน การเจาะด้วยเลเซอร์สามารถอัตโนมัติได้ง่าย แต่ข้อเสียคือจะเกิดความเครียดบนพื้นผิวด้านใน
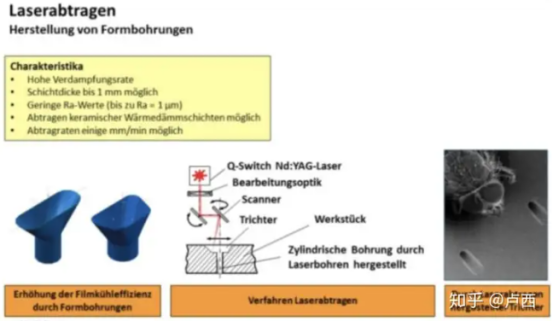
หางของสเตเตอร์เทอร์ไบน์ (ผลึกเดี่ยว ไม่เกี่ยวข้อง) จำเป็นต้องเจาะรูระบายความร้อนเพื่อรองรับโรเตอร์เทอร์ไบน์ในลำดับถัดไป รูนี้มีความบางและยาวมากจนทนแรงภายในไม่ได้ จึงทำโดยใช้วิธีการกัดกร่อนทางไฟฟ้าเคมี แน่นอนว่าสิ่งเหล่านี้ไม่ใช่กฎตายตัว และบริษัทต่าง ๆ มีวิธีการประมวลผลที่แตกต่างกัน
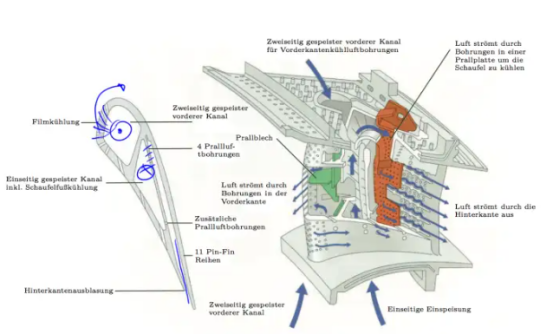
หลังจากทำเสร็จแล้ว จะได้ใบพัดกังหันคริสตัลเดี่ยวมาหนึ่งชิ้น แต่ยังไม่ได้เคลือบเลย ใบพัดกังหันสมัยใหม่จำเป็นต้องมีชั้นเคลือบกันความร้อนที่ทำจากซิร์โคนิยา (Zirconia) เป็นเซรามิกออกไซด์ของซิร์โคนิยา เนื่องจากเป็นเซรามิก มันจึงเปราะบางในระดับหนึ่ง เมื่อกังหันทำงาน หากเกิดการเปลี่ยนรูปเล็กน้อย ชิ้นงานอาจลอกออกทั้งหมด และใบพัดกังหันจะละลายทันที สิ่งนี้เป็นสิ่งที่ Hangfa ยอมรับไม่ได้เด็ดขาด
จากนั้นมีกระบวนการ EB-PVD (Electron-beam physical vapor deposition) หรือวิธีการไอน้ำตกผลึก
แน่นอนว่าก่อนการทำยังมีหลายชั้นของวัสดุอื่นๆ เช่น การชุบแพลทินัม (แพลทินัม) การพ่นพลาสมา และยังมีอีกชั้นหนึ่งที่ใช้เสริมความแข็งแรงให้ซิร์โคนิยาและยึดเหมือนกาว แน่นอนว่าแต่ละบริษัทมีความแตกต่างกันเล็กน้อย และพวกมันไม่ได้คงที่
ขั้นแรก ปืนอิเล็กตรอนปล่อยลำแสงอิเล็กตรอน ซึ่งถูกนำทางโดยสนามแม่เหล็กและชนกับวัสดุเซอร์คอนเนีย เมื่อเซอร์คอนเนียถูกโจมตีด้วยอิเล็กตรอน จะกลายเป็นสถานะแก๊ส และแก๊สเซอร์คอนเนียจะถูกนำทางไปยังพื้นผิวลำมีดเพื่อเริ่มการเจริญเติบโต เซอร์คอนเนียจะเติบโตเป็นแท่งเล็กๆ ที่มีเส้นผ่านศูนย์กลาง 1 ไมครอน และความยาว 50 ไมครอน โดยครอบคลุมพื้นผิวของใบมีดอย่างหนาแน่นโดยไม่มีรูพรุนที่เคลือบไว้ เนื่องจากไม่ใช่วัสดุเซรามิกชิ้นเดียว แท่งเล็กๆ สามารถเคลื่อนไหวได้เล็กน้อยเมื่อเทียบกันโดยไม่ลอกออกทั้งหมด ซึ่งแก้ไขปัญหาความล้มเหลวที่เกิดจากการเปลี่ยนรูป
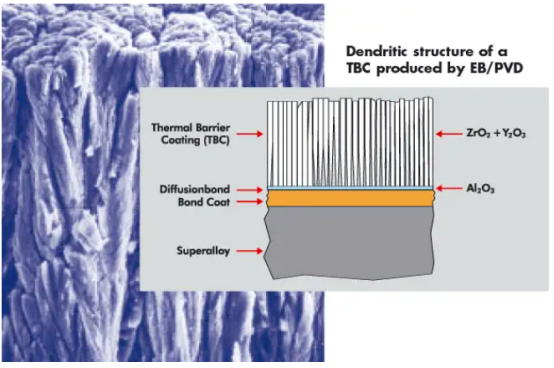
เซอร์โคนิยามีความแข็งสูงมากและมีการนำความร้อนต่ำมาก ซึ่งสามารถสร้างความชันของอุณหภูมิที่สูงมากได้ระหว่างแผ่นฐานนิกเกิลกับกระแสน้ำร้อนในแกนกลาง โดยมีการระบายความร้อนภายในและการระบายด้วยฟิล์มอากาศ ใบพัดจึงสามารถทำงานได้นานด้วยความแข็งแรงและความน่าเชื่อถือสูงในสภาพแวดล้อมที่สูงกว่าอุณหภูมิการหลอมเหลวของตัวเองอย่างมาก
ในตอนนี้ พื้นผิวของใบพัดเสร็จสมบูรณ์แล้ว เพื่อให้เข้ากับล้อเทอร์ไบน์ ใบพัดยังต้องการโครงสร้างรากใบแบบสามเหลี่ยมหรือแบบไม้สลัก
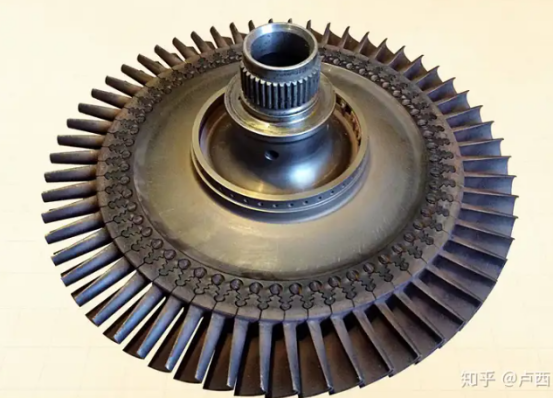
ตามที่กล่าวมาข้างต้น แต่ละใบพัดของเทอร์ไบน์ต้องทนต่อแรงเหวี่ยงมากกว่าสิบตันเมื่อทำงาน และรากใบพัดก็จำเป็นต้องถูกประมวลผลอย่างละเอียดอ่อนด้วย เนื่องจากโลหะผสมซุปเปอร์อัลลอยด์ที่มีฐานเป็นนิกเกิลมีความแข็ง ทนทานต่ออุณหภูมิสูง และยากต่อการแปรรูปมาก
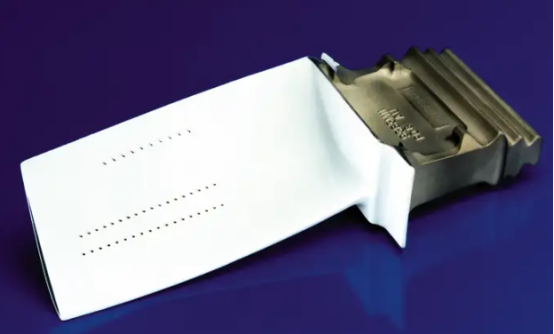
รากใบพัดถูกเจียระไนออกมา ใบพัดถูกตรึงด้วยเครื่องมือเฉพาะ และล้อเจียระไนบนและล่างที่มีรูปทรงตรงข้าม (แม่พิมพ์) จะทำการเจียระไนเข้าไป
สิ่งนี้จะทำให้จานขัดล้มเหลวอย่างรวดเร็ว ดังนั้นจึงเพิ่มจานขัดเพชรแบบบวกไว้ด้านนอกของจานขัดทั้งสองเพื่อขัดจานขัดอย่างต่อเนื่องเพื่อให้มันทำงานได้ เครื่องจักรกลใช้หุ่นยนต์ในการติดเพชรสำหรับจานขัด
หลังจากกระบวนการและการตรวจสอบเหล่านี้แล้ว ใบมีดก็พร้อมใช้งาน มันเป็นเพียงส่วนหนึ่งของเครื่องยนต์เครื่องบิน และเครื่องยนต์เครื่องบินก็เป็นเพียงโมดูลหนึ่งในเครื่องบิน