Лопатка турбіни є ключовим компонентом гарячого кінця газової турбіни, дослідження та виробництво якої є важливою ознакою масштабу розвитку та технічного рівня промисловості країни. Розглядається останній прогрес у сфері технологій виготовлення лопаток газової турбіни. На основі досліджень наукової групи представлений прогрес у галузі напрямного залізнення лопаток газової турбіни та визначено напрямки подальшої роботи.
1 Технологія напрямного залізнення
Технологія напрямного залізнення відноситься до технології, яка створює температурний градієнт у певному напрямку шляхом принуджених засобів під час процесу залізнення, щоб залізнення відбувалося у певному напрямку. У процесі залізнення металу існує температурний градієнт у конкретному напрямку між затвердженою частиною та неметалевим розчином, який не затвердjęв, що призводить до залізнення металу у напрямку, протилежному до теплопровідності. Використовуючи технологію напрямного залізнення, можна отримати стовпчасті кристали або одно kristal з певним орієнтацією, а також підготувати стовпчастий або одноkristalний лез, значно покращуючи його властивості.
У кінці 1960-х років, Верснайдер та ін. застосували технологію напрямкового залізнення до виробництва супeralloys, що краще контролювало орієнтацію зерен структури залізнення, вилучило поперечні межі зерен, що значно покращило механічні властивості супeralloys. Після десятиліть досліджень технологія напрямкового залізнення розробила метод екзотермічного порошку (EP), метод пониження потужності (PD), метод високоскоростного залізнення (PD), традиційні технології, такі як HRS [12] і охолодження рідкою металом (LMC). На даний час метод високоскоростного залізнення та метод охолодження рідкою металом широко використовуються.
1.1 Метод високоскоростного залізнення
Метод високоскоростного залізнення — це спосіб, при якому відливки рухаються у одному напрямку поступово від регіону високої температури, щоб досягти однонаправленого залізнення. Цей метод вирішує проблему поступального зменшення градієнта температури під час процесу залізнення. Принцип високоскоростного методу залізнення показаний на Рисунку 1(a). На дні печі встановлена термоізоляційна перегородка, а на перегородці відкрито відверстя трохи більше за відливку. Всередині печі підтримується нагрівання. Під час процесу залізнення металу, оболонка повільно опускається, так що частина металу, яка виявилася ззовні, починає охолоджуватися і залізнюватися, тоді як розплавлений метал, розташований всередині печі, залишається у нагрітому стані, таким чином створюючи осьовий градієнт температури. Метод високоскоростного залізнення має високий і стабільний градієнт температури та швидкість охолодження, і можна отримати довгу стовпчасту кристалізацію та мелку структуру, що значно покращує механічні властивості відливок, але градієнт температури цього методу все ще недостатній, і під час однонаправленого залізнення великих та товстих відливок все ще можуть виникати дефекти відливок, такі як фарфорування та забруднення.
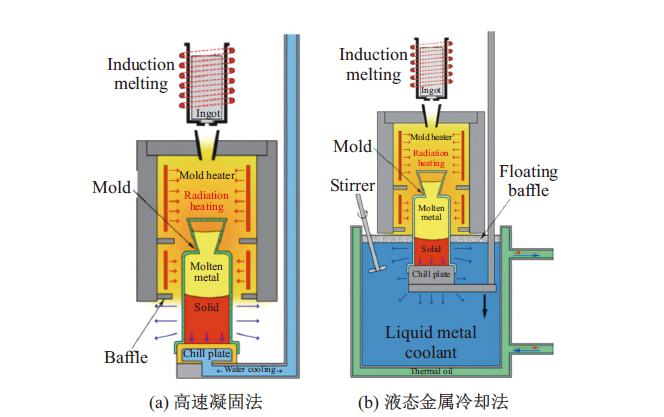