Prinsippet for hvordan høytrykks-turbinytter på flymotorer fremstilles er veldig enkelt, men de ulike parametrene i denne prosessen krever mange eksperimenter for å oppnå parameterne til hver node, sammensetningen av hjelpe-materialer, og mye lykke.
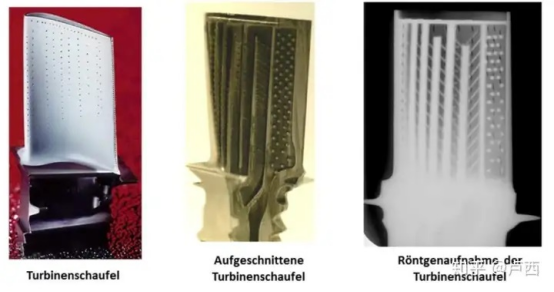
Først trenger høytrykks-turbinyttene komplekse interne kjøleluft-kanaler (se figuren nedenfor). Først lages de interne kjøleluft-kanalene (uten kjøleluft-hull, som vil bli diskutert senere). Deretter formes vaksmodellen med en spesiell keramikk for å danne kanalene.
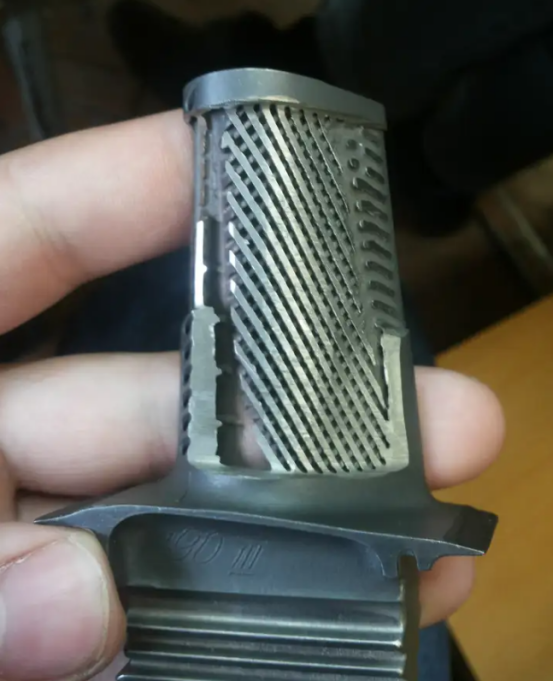
Etter å ha fått denne keramiske luftveimolden, setter du den sammen med bladets ytermold og legger den i kastingsovnen. Den smeltede superalloy* går inn i moldhulen fra topp til bunn (inkludert keramisk luftveisinermold og voksmoldet). Det er veldig krævende å lage uendelig mange lag av dekkinger mellom hver moldlaging. Tyske selskaper bruker roboter for å gjøre det, og det ser ut som om Russland fortsatt bruker tantes pensler. Disse dekkingene bestemmer direkte kvaliteten på kastingen, og toleransekraften er ekstremt lav.
På dette tidspunktet vil kastemaskinen strengt kontrollere temperaturen på den smeltede superalloyen, og deretter la den solidifisere på en horisontalflate (det vil si, veksten av krystallene), fra bunn til topp, når krystallene vokser i spiral (krystallvelger), presser de og velger hverandre ut, og til slutt vil bare én krystall som er nærmest den forhåndsbestemte retningen bli igjen, og denne krystallen vil fortsette å vokse oppover.
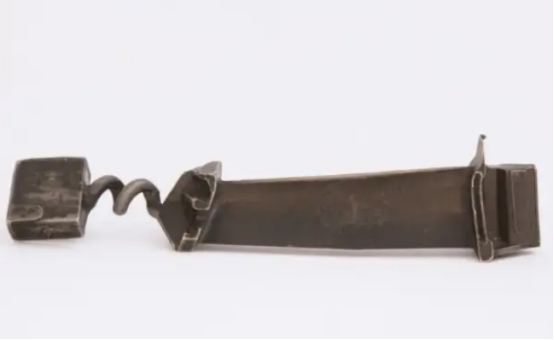
Fordi høytrykksskakken må rotere mer enn 10 000 ganger, blir hver del utsatt for mer enn 10 ton sentrifugalkraft, og fordi styrken på nikkelkristaller i hver retning er forskjellig, må dens diagonal (den sterkeste retningen) være innenfor 10 grader av sentrifugalkraftens retning. (Noe tillegg å si, den enkeltrettede nikkelbaserede alleier som brukes i lavtrykksturbinsrotoren krever kristallretning, men ikke bare én kristall, fordi smeltepunktet til enkelkristall er 50K høyere enn det til polycrystall (inkludert enkeltrettede kristaller)).
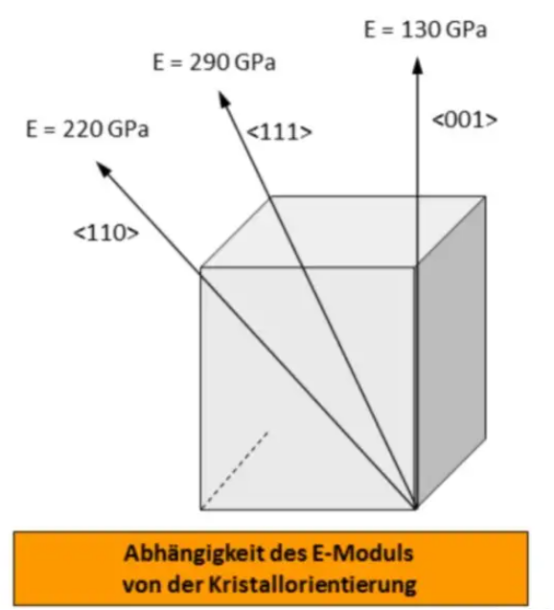
Produksjonsrendelsen er ikke høy. Så vidt jeg vet, har mange fremragende nøyaktig gjøtskefabrikker i Tyskland prøvd denne prosessen og til slutt gått i konkurs. Terskelen er virkelig for høy.
Til slutt får man det ferdige produktet, og en spesialalkali brukes for å opplese keramikkveivformen som er igjen i veien for å lage kjølevansker. Det finnes elektro-oppløselige vansker og elektrokjemiske vansker. De vanligste vanskene lages av laser. Formen på vanskene er også veldig komplisert. Deretter er det elektroplateringsoverflating, som også er et stort kunnskapsfelt.
Bildet nedenfor viser polycrystall på venstre side, enkrettskristall i midten, og enkelkristall på høyre side.
Likevel, etter gjettformingen har loddene ikke luftåpningene som forbinder den indre kjøleluftledningen med loddoverflaten. Dette gjøres vanligvis med laser. Fordi kjøleluften har mistet mye trykk når den trekkes fra høytrykkskompressoren og strømmer fra den tomme akse til høytrykksturbinen, selv om det sentrale luftstrømmen også mister trykk når den passerer gjennom forbrenningen, og prosessen fra aksen til loddene har en viss sentrifugalkomprimerings- og trykkforsterkningseffekt, krever det fortsatt et høyere statiske trykk for å føre kjøleluften mot loddoverflaten. I dette øyeblikket trengs en åpning med en utvidet korsnivå for å håndtere kjøleluften, redusere dynamisk trykk og øke statisk trykk, og deretter fører kjøleluften det varme sentrale luftstrømmen unna loddoverflaten (mye tull). Dessuten vil for høy fart føre til at kjøling blir direkte injisert i sentralen luftstrøm, og den har en annen oppgave, nemlig å danne et lag av kjølelufthinne på loddoverflaten for å beskytte loddet, noe som krever reduksjon i fart og trykkforøkelse.
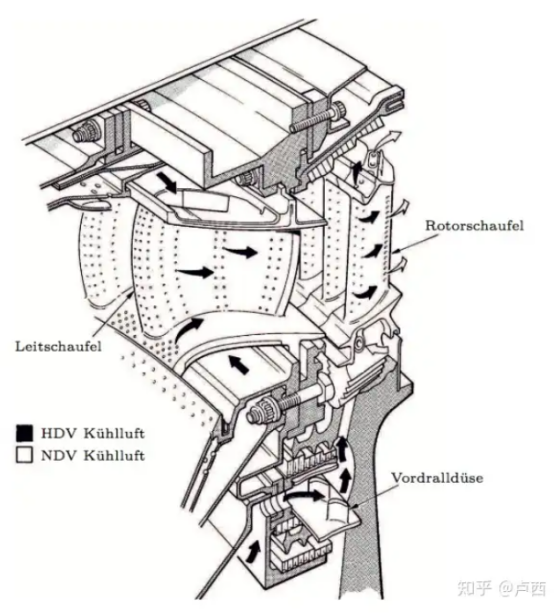
Derfor må denne typen hull optimalisere geometriske form for ulike posisjoner. Laserboring kan lett automatiseres, men ulempen er at det vil oppstå interne overflateresser.
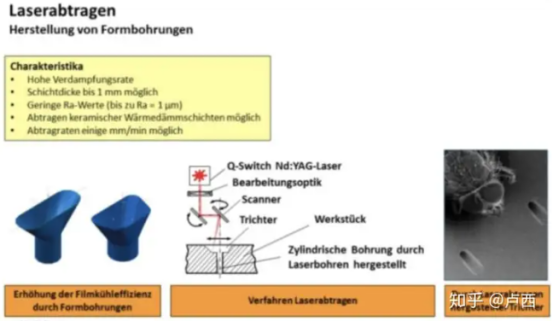
Haleen av turbine-stator (enkrysallinær, av temat) trenger å få boret veklingskjølingshull for å tjene den etterfølgende turbinrotoren. Dette hull er ekstremt slank og kan ikke tåle interne spenninger, så det lages ved bruk av elektrokjemisk korrosjon. Selvfølgelig er disse ikke absolutte, og ulike selskaper har ulike bearbeidningsmetoder.
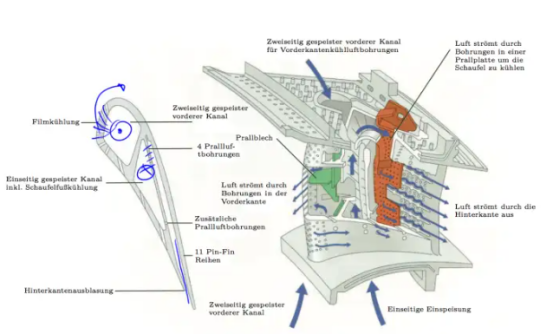
Etter å ha gjort dette, har man fått en enkrysallin turbineblad, men det er ennå ikke dekket. Moderne turbineblader krever et lag av zirkonia varmebarrieredekking, et zirkonia oksid keramikk. Fordi det er keramikk, er det i visning grad sprøyt. Når turbinen virker, hvis det er en liten deformasjon, kan hele stykket løsne, og turbinebladene vil smelte umiddelbart. Dette er absolutt uakseptabelt innen Hangfa.
Deretter er det EB-PVD prosessen (Elektronstråle fysisk dampavsetting), en dampavsetningsmetode.
Selvfølgelig er det mange lag av andre materialer før man lager det, som platinbehandling (platin), plasma spray osv. Det finnes også et lag for å forsterke zirkonia og lime det fast som lim. Selvfølgelig finnes det små forskjeller mellom hver selskap, og de er ikke statiske.
Først skutter elektronkjelsen ut en elektronstråle, som ledes av det magnetiske feltet og treffer zirkonia-underlaget. Underlaget som blir bombardert av elektronene vil gå over i en gassform, og den gassformige zirkonia ledes til bladets overflate for å begynne å vokse. Zirkonia vil vokse til små staver med en diameter på 1 mikron og en lengde på 50 mikroner, kraftig dekkende bladenes overflate uten å dekke poremne. Fordi det ikke er et helhetlig keramisk stykke, kan de små stavene bevege seg lite relativt til hverandre uten at hele delen løsner, noe som løser problemet med feil forårsaket av deformasjon.
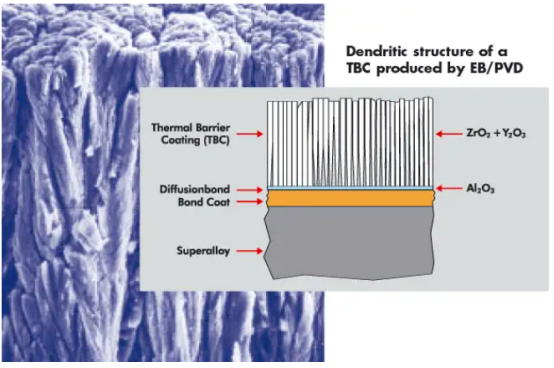
Sirkonia har ekstremt høy hardhet og ekstremt lav varmeledningsevne, hvilket kan oppnå en veldig bratt temperaturgradient mellom nikkelsubstratet og den varme kjernen av luftstrømmen. Med intern kjøling og luftfilmkjøling kan skiven fungere i lang tid med høy styrke og høy pålitelighet i et miljø mye høyere enn sin egen smeltepunktstemperatur.
På dette tidspunktet er skiveoverflaten ferdig. For å passe inn i turbinhjulet trenger skiven også en fyrstestruktur eller mortis-og-tendongrunn.
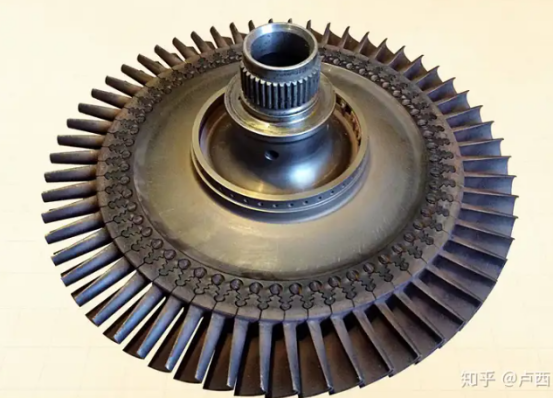
Som nevnt ovenfor, motar hver turbinskive mer enn ti tonn sentrifugalkraft under drift, og skivehælen må også behandles meget nøye. Nikkelbasert superlegeme er veldig hardt, motstandsdyktig mot høy temperatur og veldig vanskelig å bearbeide.
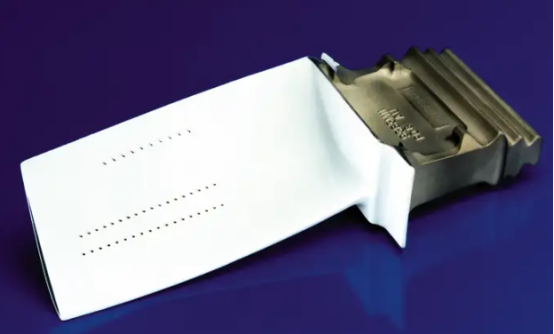
Skivehælen blir slått ut. Skiven holdes fast av et spesielt fixture, og de øverste og nederste slipehjulene med motsatt geometri (hunkjemønster) sliper inntil.
Dette vil forårsake at sjøingshjulet fort faller i stykker, så et positivt diamantsjøingshjul legges til på utsiden av de to sjøingshjulene for å sjøie kontinuerlig på sjøingshjulet for å holde det fungerende. De industrielle diamanene på diamanthjulet er limt på av roboter.
Etter disse prosessene og inspeksjonen er bladen klar til å arbeide. Det er bare en del av en flymotor, og en flymotor er bare et modul på et fly.